Overview
As the world continues to shift away from fossil fuel based internal combustion engines to clean and green electric vehicles (EVs), there are several key factors for scaling up the EV ecosystem to meet global net zero goals. The availability of sufficient lithium supply for EV batteries is at the forefront of these critical issues.

This article provides an overview of the global challenges and constraints around simply increasing the mining of more new lithium and details the importance of developing better recycling, along with an exploration of how advanced battery design practices can help improve recycling processes.
The Importance of Lithium for Achieving Net Zero Goals
According to the International Energy Agency (IEA), approximately 2 billion EVs will need to be on the road by 2050 to meet global net zero goals. However, even with the rapid ramp up of production in recent years, there were only about 10 million EVs sold in 2022 according to EV Volumes.
With this current relatively low level of EV production already straining the supply chains for newly mined lithium, the projected goal to reach 2 billion EVs puts lithium availability squarely on the critical path for success. Credit Suisse projects that lithium demand will triple in the near term by 2025.

Mining new lithium is also subject to various constraints, including:
- Limited Reserves: Lithium is not an abundant resource globally. While lithium deposits exist in various parts of the world, the economically viable reserves are limited. The concentration of lithium in ore bodies is relatively low, making it necessary to mine large quantities of ore to extract enough lithium.
- Environmental Impact: Lithium mining can have significant environmental impacts. Traditional mining methods, such as open-pit mining, can lead to habitat destruction, soil erosion, and water pollution. Additionally, lithium extraction techniques, such as evaporation ponds, can have adverse effects on local ecosystems and water resources. Meeting stringent environmental regulations and mitigating these impacts can increase the costs and challenges associated with lithium mining.
- Energy Intensity: The extraction and processing of lithium can be energy-intensive, which contributes to greenhouse gas emissions and may counteract some of the environmental benefits of using lithium-ion batteries in electric vehicles. Developing more energy-efficient mining and extraction technologies is crucial to reduce the carbon footprint associated with lithium production.
- Social and Human Rights Concerns: Lithium mining operations often take place in regions with indigenous peoples and sensitive ecosystems, so extraction can impact local communities, cultural heritage, and traditional livelihoods. Ensuring the rights and well-being of affected communities, as well as addressing social concerns, such as fair labor practices and responsible mining standards, is essential for sustainable lithium mining.
- Infrastructure and Supply Chain Challenges: Expanding lithium mining requires the development of adequate infrastructure, including transportation, energy supply, and water resources. Some lithium deposits are in remote areas, which can present logistical challenges for extraction and transport. Additionally, building a secure and resilient supply chain for lithium involves establishing refining and processing facilities, as well as secure transportation routes, which is complex and time-consuming.
Given these constraints, it becomes increasingly important to explore alternative sources of lithium, such as lithium recovery from recycling processes and the development of more efficient lithium extraction methods.

Technology Approaches for Improving EV Battery Sustainability
As a leading innovator in creating solutions to support the EV revolution, ENNOVI has developed several breakthrough technologies that provide EV manufacturers with customizable and highly scalable methods for optimizing production volumes, reliability, and sustainability.
Key among these is our Cell-PLX™ battery interconnect system, which consists of thin, lightweight, ultra-flat and robust current collectors that are designed to help EV-makers overcome the challenges of customizing reliable battery connections. With our patented U-Turn design innovation, Cell-PLX™ achieves excellent current density spread and low-loss energy transfer. This is because the energy flow is remarkably better organized as it moves from the positive to the negative terminal, across just one single conductor layer. This enables optimal battery performance, longer battery lifespan and enhanced drive range.
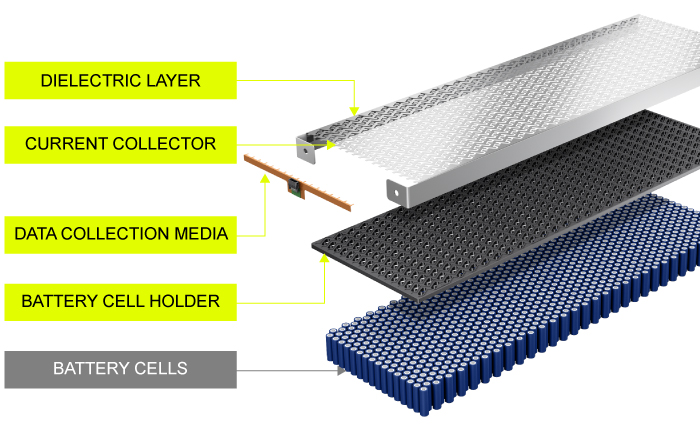
During the current collector assembly process, the top and bottom current collectors, control board, interconnects, dielectric layers, cell holders and individual cells are all brought together in a highly efficient and robust manner that supports high-volume manufacturing and can be adapted for virtually any battery size, power requirements and configuration.
As discussed in the following section, Cell-PLX™ also provides a highly adaptable basis for improving the ability of EV battery designs to support long term sustainability and offset lithium availability constraints.
Reduce, Reuse, Repair, Recycle
Having already set the standard for efficient and adaptable assembly of EV batteries, the Cell-PLX™ technology stack is also setting the stage for future improvements to both extend the useful life of batteries and enhance the ability to repair, reuse and recycle lithium-ion batteries.

Enhancing the Interconnect Removal and Reconnection Processes
Now that the widespread deployment of Cell-PLX™ by many EV makers has streamlined and standardized the assembly and interconnection of battery cells, modules and overall battery packs, the next step is to build on that standardized interconnection process to make it even more sustainable.

Although it is fast, automated, and scalable, the laser welding of interconnects currently used in EV battery implementations to attach battery cells and packs is problematic, because the aluminum connections are permanently welded to the battery terminals. This means destructive methods are required to access the battery pack for recycling to be conducted.
This not only adds cost and time to the recycling process; it also makes it impractical to remove the interconnect element so that individual Li-Ion cells can be replaced, which means good cells within the battery pack are unnecessarily wasted. As a result, the recycling process ends up sub optimally recovering lithium from many good cells that still have useful life.
ENNOVI is working closely with EV makers, battery cell manufacturers, and recyclers to map out a forward technology path that can replace the use of permanent connection methods, such as laser welding, with “weldless” processes that support clean and easy disconnections. By making recycling processes simpler, a circular economy can be created, with harmful substances not polluting the environment and the limited availability of certain materials being mitigated. Furthermore, by not having to dispose of entire battery packs (but just swapping faulty cells instead) the replacement costs involved are greatly reduced.
Minimizing Material Waste
The second key focus area after elimination of permanent welding is to reduce other materials within the overall battery design, such as the plastic carriers that were helpful in maintaining alignment during the welding process. This not only simplifies manufacturing processes and lowers Bill of Materials cost; it also streamlines the recycling procedures and reduces material wastage.

Enhancing Functionality with Complementary Technologies

The weldless, clip-on interconnects and simplified overall battery design also open the door for effective integration of related functionality, such as Battery Management System (BMS) monitoring points.
In addition to enabling better management of battery charging, usage monitoring, lifecycle length, and range per charge, these added functions also help avoid wasting lithium.
For example, the ability for EV makers to use targeted monitoring to identify problem cells and replace them on an individual basis means that battery packs can be refurbished with new cells that extend their useful lifecycles. Instead of decommissioning the entire battery pack and having to lose or recover the lithium from all the good cells, manufacturers will be able to simply exchange failed cells with new ones.
Summary

Improving electric vehicle (EV) battery design can significantly facilitate the recycling process by considering a range of factors including:
Standardization: Designing batteries with standardized components and interfaces, such as Cell-PLX™, enables easier disassembly and separation of different materials during recycling. It allows for efficient removal of hazardous components and enhances the recovery of valuable materials.
Modular Design: Implementing a modular design approach allows for the disassembly of batteries into smaller units or modules. This makes it easier to identify and replace faulty or degraded components, reducing the need for complete battery replacement. Modular designs simplify the recycling process by enabling the selective removal of specific modules or cells for recycling, rather than dismantling the entire battery pack.
Material Selection: Battery design should consider the use of environmentally friendly and recyclable materials. Avoiding or minimizing the use of hazardous or hard-to-recycle substances simplifies the recycling process and reduces potential environmental impacts. Designers can explore alternative materials or develop innovative material compositions that are easier to recycle without compromising performance.
Easy Access Points: Designing batteries with easy access points for disassembly and recycling can streamline the process. Incorporating features like removable covers or access panels simplifies the removal of battery modules or cells, allowing for more efficient recycling operations.
Design for Disassembly: Considering the ease of disassembly during the design phase, as described in this article, can significantly reduce the time and effort required for recycling. Designing batteries with fewer permanently welded connections can facilitate disassembly and separation of components during recycling, and/or replacement of failed cells to extend battery lifecycles.
Battery Tracking and Tracing: Implementing tracking systems to monitor battery usage, performance, and end-of-life information can assist in the recycling process. It enables effective identification of batteries at the end of their life cycle, ensuring they are properly collected and directed to appropriate recycling facilities.
Collaboration with Recyclers: Collaboration between battery manufacturers and recycling facilities is crucial. By involving recyclers in the design process, manufacturers can gain insights into the challenges and requirements of the recycling industry. This collaboration can lead to design optimizations that better align with the recycling infrastructure and processes, improving overall recycling efficiency.
By considering these factors, battery designers can contribute to the development of batteries that are easier to recycle, reducing costs, improving resource efficiency, and supporting the transition to a more sustainable and circular economy.